Suite à une orientation stratégique de l’entreprise de ne plus utiliser notamment d’emballage plastique, il a été décidé de «repenser» les lignes d’assemblage et d’emballage en réduisant les gaspillages et en introduisant une démarche d’amélioration continue.
Accompagner l’équipe projet pour :
- Former aux basiques du Lean Manufacturing.
- Insuffler une culture « flux » et d’amélioration continue.
- Elaborer et concevoir de nouvelles lignes en utilisant les 9 étapes de la méthodologie de conception de ligne.
- Rendre autonome les équipes lors de la mise en place de nouvelles lignes.
- Nouvelles lignes mise en place dans le délai imparti.
- Autonomie des équipes projets.
- Mise en place d’une animation de la performance pour améliorer les résultats grâce à la démarche d’amélioration continue.
- Concepts du Lean Manufacturing partagés et appréciés par les équipes de production.
Avant
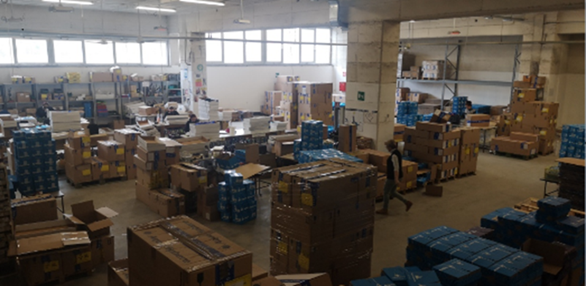
Après
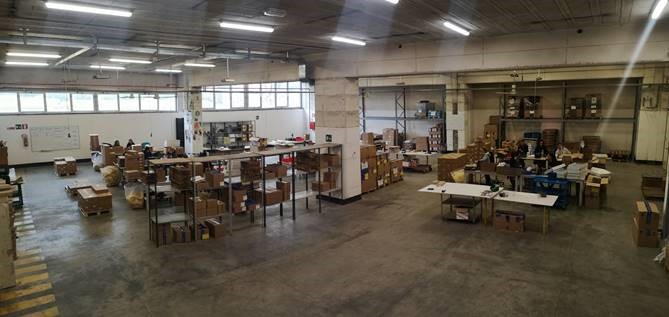
- Autonomie de Technisub pour la conception de futures lignes.
- Atteindre les objectifs de productivité grâce à l’amélioration continue.
Au début du cours Lean, nous étions sceptiques à l’idée d’abandonner les méthodes de production développées au fil des décennies, mais dès que nous avons mis en pratique les nouvelles méthodologies à travers deux lignes pilotes, nous avons immédiatement vu le potentiel d’amélioration. Jour après jour, l’efficacité et la participation active au projet de tous les opérateurs impliqués ont augmenté. À ce jour, les principaux avantages trouvés jusqu’à présent sont : Une meilleure gestion de l’entrepôt et le flux de composants vers les lignes de production, mis en œuvre par la création du supermarché et l’étude des fournitures horaires nécessaires; Une amélioration de la commande et de la gestion des espaces dans les sites d’assemblage et d’entrepôt; Une amélioration de la réactivité aux problèmes de fabrication dus à des défauts dans les composants ou des procédures de production; Une augmentation de l’efficacité de la production et du contrôle des lignes de production; Une participation proactive à la culture d’amélioration continue de tout le personnel impliqué dans ces nouvelles lignes. Un dernier point qui nous donne de l’espoir : nous savons que le travail accompli jusqu’à présent n’est pas un point d’arrivée mais le début d’une voie d’amélioration pour les productions actuelles et les projets futurs.